Enhancing Efficiency and Top Quality With Modern Steel Stamping Methods
In the world of production, the quest for improved productivity and high quality continues to be a perpetual goal. Modern steel marking methods have actually arised as a critical device in attaining these objectives, reinventing the sector through a blend of sophisticated modern technologies and innovative methods. As the needs for accuracy and efficiency continue to intensify, the assimilation of automation and electronic tools into the metal marking procedure has actually come to be critical. Nevertheless, the real action of success exists not only in the adoption of these modern methods however additionally in the thorough control of quality standards throughout the production cycle. By discovering the detailed interaction in between modern technology, automation, and accuracy in steel marking, a path towards unequaled performance and top quality guarantee unfolds.
Advantages of Modern Metal Marking
Modern steel stamping deals countless benefits in terms of performance, accuracy, and cost-effectiveness in the manufacturing industry. Among the crucial benefits of modern-day metal stamping is its capacity to effectively produce high quantities of complicated metal components with constant quality. This procedure eliminates the demand for several operations as it can execute different jobs such as blanking, piercing, forming, and reeling in a single procedure.
Furthermore, modern-day metal marking allows manufacturers to attain tight resistances and precise requirements, guaranteeing that each component satisfies the called for requirements. This high degree of precision leads to minimal product waste, reduced rework, and general better product top quality.
Additionally, contemporary steel stamping is a cost-efficient manufacturing approach. The automation and high-speed abilities of modern-day stamping devices bring about lower labor expenses and faster manufacturing rates. This effectiveness not just reduces manufacturing expenditures but likewise allows firms to meet tight manufacturing target dates and deliver products to the marketplace faster. Essentially, modern-day steel marking offers a competitive edge to makers looking to enhance efficiency and high quality in their procedures.
Advanced Technologies in Metal Stamping

Another vital innovation transforming metal marking is making use of servo presses. Unlike traditional mechanical presses, servo presses supply higher control over the speed and pressure applied throughout the stamping process. This control not only boosts the top quality of the stamped parts but also lowers material waste and energy usage.
Additionally, developments in simulation software program have actually enabled suppliers to practically test and maximize the stamping procedure before physical production starts. This online prototyping aids determine possible issues beforehand, resulting in set you back savings and faster time-to-market for brand-new items. In general, these innovative technologies in steel marking are driving unprecedented degrees of performance and high quality in the sector.
Improving Efficiency With Automation
The assimilation of automated systems has substantially boosted the efficiency of metal marking procedures. Automation in metal stamping procedures supplies a myriad of benefits, including boosted manufacturing rates, improved accuracy, and lowered labor costs. By utilizing robotic arms and computer-controlled equipment, jobs that were formerly time-consuming and susceptible to mistakes can currently be implemented swiftly and with amazing precision.
Automated systems have the ability to take care of recurring tasks with consistency, resulting in higher efficiency levels and minimized cycle times. This boosted performance not just brings about cost savings but also ensures a more streamlined and reputable production process. Furthermore, automation enables real-time tracking and data collection, allowing producers to recognize and deal with issues quickly, further optimizing the overall efficiency of steel marking procedures.
Additionally, automation promotes a safer working environment by reducing the demand for hand-operated treatment in dangerous tasks. By delegating these duties to automated systems, employees can concentrate on more complex and value-added tasks, adding to a more efficient and effective process in the metal marking market.
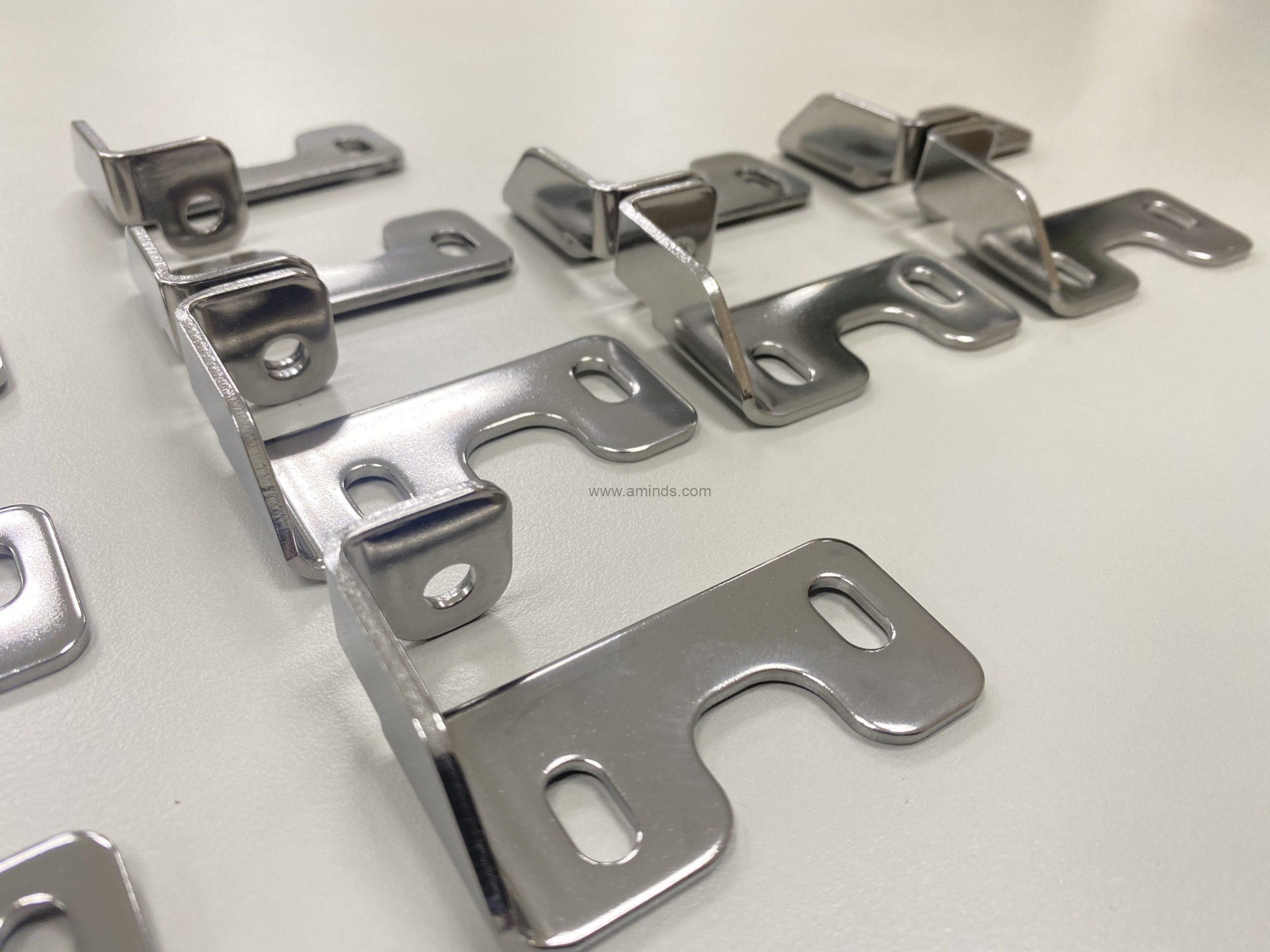
Quality Control Actions in Marking
Executing stringent quality assurance procedures is critical in ensuring the accuracy and consistency of steel stamping procedures. By developing robust top quality control procedures, manufacturers can recognize and correct any kind of variances or defects in the stamped components, ultimately boosting product top quality and client satisfaction. Among the primary quality assurance measures in steel stamping is carrying out normal evaluations throughout the manufacturing cycle. These evaluations entail checking the measurements, surface finish, and total integrity of the stamped elements to verify compliance with the specific requirements.
Furthermore, applying advanced innovations such as automated vision systems can additionally boost the quality control process by allowing real-time surveillance and discovery of any anomalies during production. These systems use cams and computer system formulas to inspect get rid of high precision and Get the facts accuracy, reducing the danger of flaws getting away right into the end product.
Furthermore, developing a thorough documents system that tapes high quality control data and evaluation results is essential for tracking efficiency patterns and helping with continuous improvement campaigns. By examining this data, manufacturers can identify potential locations for optimization and carry out rehabilitative activities to enhance the general quality of their stamped products.
Enhancing Accuracy With Digital Equipment
Employing electronic tools can significantly boost the precision of metal marking processes, revolutionizing the method producers achieve precision in their production. Digital devices such as computer-aided design (CAD) software program permit the creation of detailed stamping layouts with exceptionally precise dimensions. By inputting comprehensive requirements into the software program, makers can ensure that each stamped item meets precise dimensional needs, minimizing mistakes and waste in the production procedure.
Furthermore, the assimilation of sensors and real-time tracking systems in marking equipment makes it possible for manufacturers to carefully monitor the stamping procedure and make immediate modifications to make certain precise results. These electronic devices offer beneficial data on variables such as pressure, rate, and placement, allowing for quick recognition and improvement of any variances from the wanted specifications.
Final Thought
To conclude, modern-day metal stamping techniques learn this here now use countless click here to find out more benefits for enhancing efficiency and high quality in making procedures. By utilizing advanced innovations, automation, quality assurance procedures, and electronic devices, firms can improve efficiency, precision, and overall performance. These developments in metal stamping not only improve production processes however likewise guarantee constant and top notch outcomes. Accepting these contemporary methods can cause considerable improvements in the manufacturing market.